even though i have purchased many button parts (over 100,000 at last count) from various sellers and distributors, they have mostly come from west bend, wisconsin. how can i know this, you ask? well, the boxes come padded and packed in crumpled newspapers from - you guessed it - west bend, wisconsin. this crumpled paper, obviously, got me thinking about where the parts were coming from in more specific terms than i had previously considered. i knew, basically, how the parts are made and i could guess at physical manufacture processes. but, i didn't know who made them. i didn't know anything about their business practices. i didn't know what happened to waste materials. i didn't know much.
until today.
taking advantage of our proximity to west bend while visiting faythe, i arranged to visit usa buttons, self-described as "the world's largest manufacturer of button making machines and parts and supplies for the button, ribbon and awards industry" (i have not bothered to try to verify this claim, as i believe that unchallenged stakes are true). regardless of their size, they are the folks creating the button parts that i have been using and they are the folks packing boxes with their local papers.
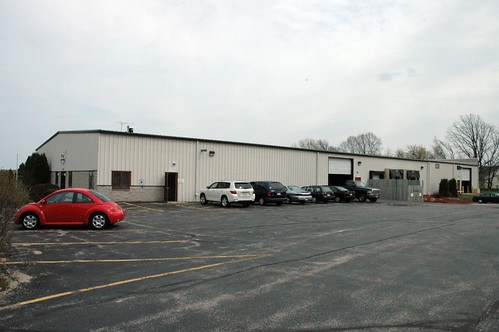
yup, this is where the magic happens. with all the indie handmade jargon floating around (peppered with small slights towards factory production), it seemed very important to me to acknowledge the relationship between factory made materials and what i do in independent art, craft and manufacture. i do this knowing full well how widespread this factory complicity is within the craft community. yarns, beads, glues, glitters, threads, needles, paper, fabric - of the things among these that can be made by hand alone, none of them are being made currently in quantities sufficient to support the ever-growing craft economy's needs.

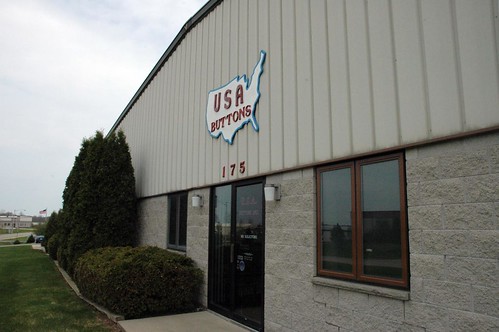
but back to west bend and the factory i have been supporting over the years. i had the delightful opportunity to chat for upwards of an hour with sales and customer service rep, margaret whatley, and operations manager, harry gramoll jr., who were both veritable fonts of information on the manufacture, history, trends and cultural climate of button machines and parts. and they indulged all of my questions with a happiness and genuine interest that this tired city girl was not expecting. it's the midwest.
a learned about the six inch button machine that harry had in his office (a technology that came to usa buttons through the acquisition of a defunct manufacturing company in connecticut). it never went into production in west bend, when harry priced out its manufacture at a raw cost almost $800 higher than the conneticut comapny's retail (hence their defunctitude, one would assume). also, a button the size of a salad plate might have limited appeal for the amount of effort and invenstment required to make it and all its coordinating parts.
margaret showed me square and rectangular machines, stack punches with interchangeable dies, and went over various techniques and quirks attached to the more complicated machines.
and harry's office boasted a button wall of old, new and novelty buttons of all sizes unlike any collection i have seen (although there must be a few).
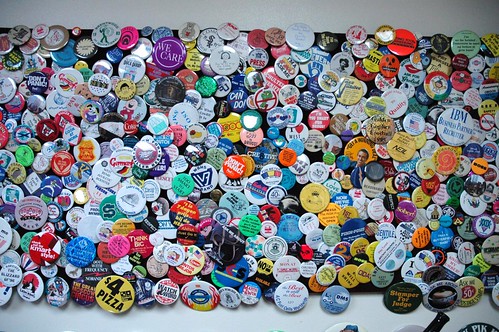


margaret and harry both purport the company to be family run, well managed, and a nice and respectful place to work. the extended family feeling of working at usa buttons came up a few times. of course, i am a client of theirs - one could guess that they would want to represent their business to me in a positive light. but the atmosphere was friendly in an unforced manner that made me believe them.
i also got down to some big question i hadn't yet had found any information about concerning the environmental responsibility of button part and machine manufacture. things were much as i had imagined in that department - all metal waste (the bulk of waste from this manufacturing process) is sold as scrap to be recycled. the mylar off-cuts go to the landfill. harry did tell me, however, that they are very committed to reducing waste in their manufacturing process and recycling off-cuts wherever possible. the waste from the plastic backing used for some products (none that i use) was recently paired with a recycling depot. harry also said that they got to the beginning stages of a potential mylar recycling contract with a man in illinois, but that it had fallen through and the man had disappeared. he also said that the mylar comes from california and that he would give another look in that direction for facilities that had the means to repurpose the difficult plastic. many of the things that makes it so well suited for button making (thinness, archival quality, toughness) also make it a challenging material to break down without burning it.
clearly, there is still growth to happen evnvironmentally. and questions of waste and recycling only represents one of many levels of environmental responsibility required to run a large scale manufacturing business. but i am happy that i know a little bit more about the products i make through margaret and harry's generosity with their time and knowledge.
oh, and this is the end of their street, below.
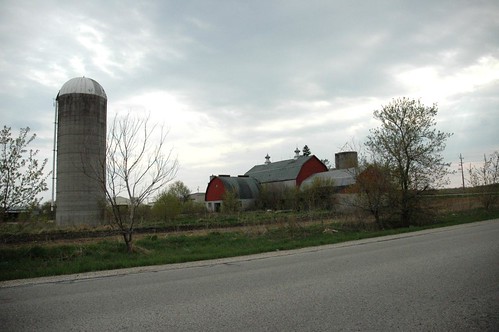
5 comments:
yeah! it's great to see behind the scenes of usa buttons, where i also have been buying button parts from for YEARS. it's so nice to be traveling (virtually) with you again...
I love the reporting! This is great! I like that you let your supplier know that it's important to you that they are environmentally responsible and it looks like they are working toward it as much as possible! As to the previous post...mmm...squeaky cheese! :)
This is an awesome story, I have never given much thought to where button parts come from before. I think it's just nice to know they are still manufactured in North America and not shipped from overseas. I'm going to pay more attention to where my button parts are coming from, from now on! Thanks!
oh, here you are.
so good to hear your voice, b-star.
I LOVE this post -- thanks for sharing the story of your field trip.
As a fellow customer of USA Buttons, it's awesome to have this behind-the-scenes peek at their company. I've never thought to go visit -- so glad your experience was a positive one!
Post a Comment